4)克劳斯尾气加氫转化催化剂活性评价
1.克劳斯尾气加氫活性评价装置
催化剂活性评价在5ml微型反应装置上进行,反应器由内径为14mm的不锈钢管制成,反应炉采用电加热方式,近似等温炉体。催化剂装填量为5ml,催化剂上部装填相同粒度的石英砂进行混合预热。采用日本岛津GC—204气相色谱仪在线分析反应器入口及出口气体中H2S、SO2、CS2的含量,采用装填GDX—301担体的色谱柱分析硫化物,柱温120℃,采用热导检测器,以氢气作载气,柱后流速28ml/min。
图1 SCOT催化剂活性评价装置示意图
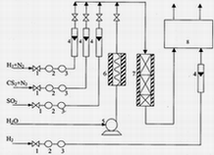
1.截止阀 2.稳压阀 3.稳流阀 4.质量流量计 5.计量泵
6.蒸汽发生器 7.反应器 8.气相色谱仪
2. 催化剂SO2加氢活性评价
试验装置经试密合格后,对催化剂进行常规干法预硫化。硫化条件为:压力为0.1MPa,体积空速为1200h-1,所用硫化气为氢气加2(v)%的硫化氢。
硫化步骤:用氮气升温,按空速调整好氮气量,以50℃/h升温至200℃,切断氮气,切换为硫化气,并调整气量,继续升温至250℃,恒温3h,待反应器出入口硫化氢平衡后,结束硫化,切换为反应气。反应气组成为SO2 1.0%、H2 6%其余为氮气。以3H2+SO2→H2S+2H2O为指标反应,考察催化剂的SO2加氢活性。气体体积空速为1200h-1,反应温度为220℃、240℃。根据下式计算催化剂的SO2加氢活性:
ηSO2= ×100%
其中M0、M1分别代表反应器入口及出口处SO2的体积浓度。
3.催化剂有机硫水解活性评价
试验装置经试密合格后,对催化剂进行常规干法预硫化。硫化条件为:压力为常压,体积空速为1200h-1,所用硫化气为氢气加2(v)%的硫化氢。
硫化步骤:用氮气升温,按空速调整好氮气量,以50℃/h升温至200℃,切断氮气,切换为硫化气,并调整气量,继续升温至250℃,恒温3h,待反应器出入口硫化氢平衡后,结束硫化,切换为反应气。反应气体积组成为CS2 0.6%、H2O30% 、H2 6%,其余为氮气。以CS2+2H2O→CO2+2H2S为指标反应,考察催化剂的有机硫水解活性。气体体积空速为1200h-1,反应温度为220℃、240℃。根据下式计算催化剂的水解率:
ηCS2= ×100%
其中C0、C1分别为反应器入口及出口处CS2的体积浓度。
4.试验结果
按照上述评价方法,每条件评价10小时,每两小时分析一次,分析结果取平均值。评价结果见表1。
表1 催化剂活性对比结果
温度/℃
|
项目
|
SL-S01
|
SL-S02
|
美国
C534
|
美国
C29
|
220
|
SO2加氢转化率,%
|
92
|
≥99
|
80
|
75
|
CS2水解率,%
|
95
|
≥98
|
78
|
72
|
|
240
|
SO2加氢转化率,%
|
≥99
|
≥99
|
93
|
88
|
CS2水解率,%
|
≥98
|
≥98
|
90
|
86
|
|
260
|
SO2加氢转化率,%
|
-
|
-
|
≥99
|
≥99
|
CS2水解率,%
|
-
|
-
|
≥98
|
≥98
|
从表1结果可以看出,两种催化剂在反应温度240℃时,二氧化硫加氢活性大于99%和有机硫水解活性大于98%(即使用色谱检测不到非硫化氢的含硫化合物),在反应温度220℃时,SL-S01、SL-S02型催化剂的二氧化硫加氢活性、有机硫水解活性仍明显优于美国的C-534催化剂和C29催化剂,其中,C-534在镇海炼化7万吨/年硫回收装置上使用,C29催化剂在金陵石化5万吨/年硫回收装置上使用。
三聚氰胺催化剂研究
一、概述:
1834年德国人利比希(Libig)在法国留学期间发现:硫酸氰钾和氯化铵反应可生成三聚氰胺。一百多年后的二十世纪五十年代,最先是美国接着是日本有了三聚氰胺的小规模生产,当时采用的原料是双氰胺法。六十年代以后,随着石油化工的迅速发展,尿素装置的大型化,为尿素法三聚氰胺提供了大量廉价原料。各国相继也新建了许多三聚氰胺生产装置。
我国三聚氰胺生产自1958年在天津建成采用双氰胺为原料的年产100吨三聚氰胺装置开始,七十年代陆续在上海、江苏、山东、四川等地建成以尿素为原料的常压法三聚氰胺装置,生产能力仅为年产150~500吨。1984年四川化工总厂引进DSM法的低压装置(年产12,000吨) ……。根据市场的需求,特别是改革开放后的迅速发展,三聚氰胺生产规模由小到大,产量由低到高,技术由粗到精,质量不断提高,开发了中国独有的半干法常压生产三聚氰胺的技术。到2004年底,据不完全统计,全国三聚氰胺生产厂发展到八、九十家,生产能力达到近六十万吨,而且都向大型化、全循环方向发展。
三聚氰胺行业在发展,三聚氰胺用催化剂也在发展。按目前三聚氰胺用催化剂消耗定额计算:每生产一吨三聚氰胺需耗(流化床磨擦破碎)15—25公斤催化剂计,全年需催化剂在12000吨以上,每个装置的第一次装填量以13吨催化剂/年产1000吨三聚氰胺装置计,约需8000吨左右。而三聚氰胺用催化剂价格每吨在10000元以上(硅铝微球每吨18000元、粗孔硅胶每吨8000元),其销售额达上亿元,经济效益十分显著。
开发三聚氰胺催化剂直接经济效益显著;间接经济效益也非常可观。在目前原材料涨价、市场竞争激烈、企业内部挖潜势在必行的形势下。对现有三聚氰胺生产企业而言,采用本公司生产的催化剂:反应温度可降40--50℃,光这一项节能达15%以上。因催化剂尿素加量比现有催化剂增加一倍以上,相当提高装置生产能力一倍,为此可节省固定投资600万以上(按年产1000吨三聚氰胺计)。由于采用我们的新型三聚氰胺催化剂,选择性高,可节省尿素1/4(以硅胶为催化剂每吨三聚氰胺需消耗尿素约4.0吨,而采用新催化剂后,每吨三聚氰胺只消耗3.2吨尿素。理论量是一吨三聚氰胺需消耗2.86吨尿素)。其它由于采用本公司生产的催化剂,付反应减少,三聚氰胺产品品位提高,精制工序简化,从而也可带来相应的经济效益。
综观三聚氰胺行业,中国生产的三聚氰胺量已占世界第一位。中国在三聚氰胺生产工艺上,在引进、消化国外先进技术的基础上已有不少创新。生产规模也向大型化、自动化发展。《清大华业》将三聚氰胺生产的软件包卖给了德国鲁奇公司,这标志着中国的三聚氰胺技术将走出国门,在国际舞台上与发达国家展开竞争!而三聚氰胺的核心技术----催化剂,却是几十年一贯制,没有进步,与国外催化剂相比有很大差距……。为了振兴民族工业,为了给三聚氰胺行业的发展提供性能优良的催化剂,本公司在原天津化工研究院开发三聚氰胺催化剂的基础上,大胆创新,广泛采用业内专家的意见,从筹建小型流化床评价装置开始,克服种种困难,开发出一种性能优良的三聚氰胺用催化剂。
1834年德国人利比希(Libig)在法国留学期间发现:硫酸氰钾和氯化铵反应可生成三聚氰胺。一百多年后的二十世纪五十年代,最先是美国接着是日本有了三聚氰胺的小规模生产,当时采用的原料是双氰胺法。六十年代以后,随着石油化工的迅速发展,尿素装置的大型化,为尿素法三聚氰胺提供了大量廉价原料。各国相继也新建了许多三聚氰胺生产装置。
我国三聚氰胺生产自1958年在天津建成采用双氰胺为原料的年产100吨三聚氰胺装置开始,七十年代陆续在上海、江苏、山东、四川等地建成以尿素为原料的常压法三聚氰胺装置,生产能力仅为年产150~500吨。1984年四川化工总厂引进DSM法的低压装置(年产12,000吨) ……。根据市场的需求,特别是改革开放后的迅速发展,三聚氰胺生产规模由小到大,产量由低到高,技术由粗到精,质量不断提高,开发了中国独有的半干法常压生产三聚氰胺的技术。到2004年底,据不完全统计,全国三聚氰胺生产厂发展到八、九十家,生产能力达到近六十万吨,而且都向大型化、全循环方向发展。
三聚氰胺行业在发展,三聚氰胺用催化剂也在发展。按目前三聚氰胺用催化剂消耗定额计算:每生产一吨三聚氰胺需耗(流化床磨擦破碎)15—25公斤催化剂计,全年需催化剂在12000吨以上,每个装置的第一次装填量以13吨催化剂/年产1000吨三聚氰胺装置计,约需8000吨左右。而三聚氰胺用催化剂价格每吨在10000元以上(硅铝微球每吨18000元、粗孔硅胶每吨8000元),其销售额达上亿元,经济效益十分显著。
开发三聚氰胺催化剂直接经济效益显著;间接经济效益也非常可观。在目前原材料涨价、市场竞争激烈、企业内部挖潜势在必行的形势下。对现有三聚氰胺生产企业而言,采用本公司生产的催化剂:反应温度可降40--50℃,光这一项节能达15%以上。因催化剂尿素加量比现有催化剂增加一倍以上,相当提高装置生产能力一倍,为此可节省固定投资600万以上(按年产1000吨三聚氰胺计)。由于采用我们的新型三聚氰胺催化剂,选择性高,可节省尿素1/4(以硅胶为催化剂每吨三聚氰胺需消耗尿素约4.0吨,而采用新催化剂后,每吨三聚氰胺只消耗3.2吨尿素。理论量是一吨三聚氰胺需消耗2.86吨尿素)。其它由于采用本公司生产的催化剂,付反应减少,三聚氰胺产品品位提高,精制工序简化,从而也可带来相应的经济效益。
综观三聚氰胺行业,中国生产的三聚氰胺量已占世界第一位。中国在三聚氰胺生产工艺上,在引进、消化国外先进技术的基础上已有不少创新。生产规模也向大型化、自动化发展。《清大华业》将三聚氰胺生产的软件包卖给了德国鲁奇公司,这标志着中国的三聚氰胺技术将走出国门,在国际舞台上与发达国家展开竞争!而三聚氰胺的核心技术----催化剂,却是几十年一贯制,没有进步,与国外催化剂相比有很大差距……。为了振兴民族工业,为了给三聚氰胺行业的发展提供性能优良的催化剂,本公司在原天津化工研究院开发三聚氰胺催化剂的基础上,大胆创新,广泛采用业内专家的意见,从筹建小型流化床评价装置开始,克服种种困难,开发出一种性能优良的三聚氰胺用催化剂。